WORKSHOP
BUILDING OUT MY WORKSHOP:
The basement space that was I had laid out for a 2-car garage and my guitar workshop was, in its previous incarnation, a garage for the original owner’s (a messenger service) delivery vehicles. It was tucked about 1 ½ meters underground, with small steel-framed opening commercial windows along one side and a concrete floor, and concrete and brick walls. Ceiling height was minimal, being exactly 2 meters (78”). It was undivided and only partially-finished, with bare-painted-brick walls. The concrete floors were textured and sealed. Just a big empty space as long and wide as our residence on the floor above. Because the living part of our loft has both radiators and in-floor radiant heating, the workshop ceiling is where the radiant heating pipes run, and it’s rough concrete over clay blocks. So, despite cold winter temperatures, the shop is usually warm enough—68 ºF—to work in, as long as I’m wearing a sweater or sweatshirt. Still, I installed a small pellet stove for heat when needed. It doesn’t get very cold here; 28 ºF at night and 35 ºF in the daytime in the coldest winter days, December through late January. We saw a tiny bit of snow our first January here in 2021; haven’t seen any since. Modena used to get 6”-12” regularly in the past. Those days seem to be over.
I had decided to divide this large space into two large areas and two smaller ones. The largest room (the workshop) was to be 30 feet long by 18 wide, and the next largest (the garage for 2 cars) would be 22 feet long by 18 wide. In between the two would be two smaller rooms—my buffing area, 6 feet long by 8 feet wide, and my spray booth, 6 1/2 feet square. Running along one side of the buffing area would be an easement about 6 feet wide for shop access.
Because lamps and outlets were not required for the space’s original use as a storage and garage area, there was exactly one bare light bulb and zero electrical convenience outlets. I purchased 12-2-meter-long flush mount LED ceiling fixtures that were only 2” tall, and mounted six rows of two each, spaced a meter and a half apart, running across the ceiling. These were wired to the single switch above the garage door, as were the machine wires and outlets. I installed several large 2 Kw voltage-reducing transformers, as some machines were easy to convert to 220 volts, and the rest, along with convenience outlets, were 110V and were tapped into these transformers. (All of my handheld tools and many smaller, low-amperage stationary tools are 110V). It took about 3 days to hang the lights and wire up the shop. It all runs on one 20A breaker through 12 gauge wiring. Oddly, this is common practice in Italy, which has its own electrical codes that differ from the EU codes.
Italian wiring takes some getting used to, but is actually much simpler than the wiring we’re used to in the USA. For residences and light industry, there is generally only one gauge of wire that is used (#12) in four colors. No thick/thin like the States. The reason for this is that when a structure is built, it is going to usually be 100% block or brick. To dig into these, just to change wiring gauge to a heavier one, is quite a hassle, so electricians here just install the heaviest gauge right from the outset when wiring a building. Like most of the EU, wire runs in plastic conduit, which is very easy to cut and fit, and some joints are glued, though compression fittings are most common. The building itself is the ground circuit. Simple unless you accidently touch a live wire to a wall and can’t figure out why you blew a breaker…
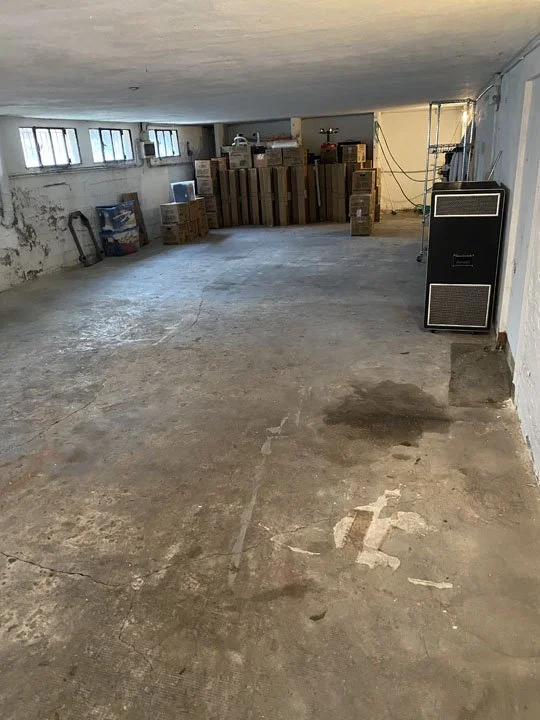



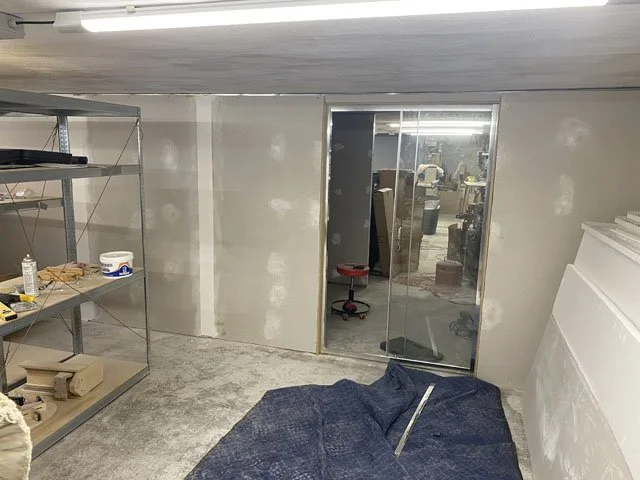
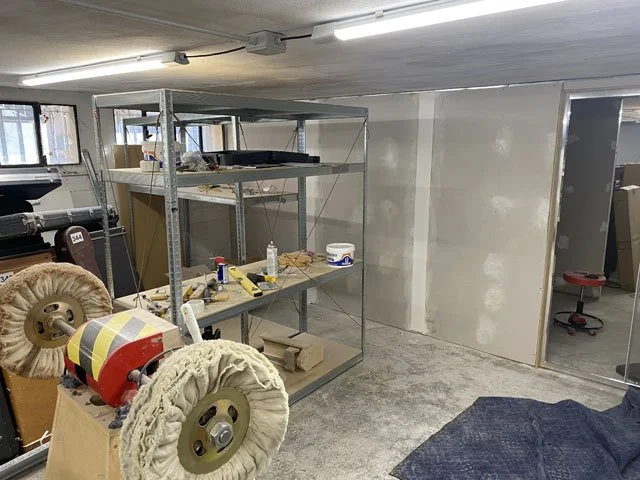
There were two space issues. The first involved framing and installing doors in walls that were only 78” tall. The second involved replacing the original, 1970-vintage garage doors, which were center-locking, side hinged steel shed doors that opened inward, which meant that every time they were opened, they took up 4 feet of my precious indoor floor space!
I ordered two sliding glass shower doors to solve the first issue, as they were 76” tall by 48” wide. One set provided access between the garage and workshop, and the other between the workshop and spray booth. I made a dimensioned sketch for a replacement garage door and ordered all three doors from our local giant building supply chain, Technomat. All three were delivered in about 3 weeks. I installed all three in one weekend. Overhead sectional (USA-type) garage doors are a rare animal in this town, but I got this one hung and a remote-controlled power opener installed and programmed the next Saturday and part of that Sunday. It worked first time, and has worked since, for the better part of four years.
I did some research on wall finishes. What we call “dry wall” in the US is called “cartongesso” here, which translates to “cardboard plaster”, It is not too often used. Our loft has two partition walls between the great room and each bedroom which are cartongesso. For the workshop, I purchased 30 sheets of a standard insulated cartongesso. This type is a standard 13mm thickness plaster board, bonded to a slab of 22mm-thick polystyrene (coffee cup) foam. It serves as both a wall finish and thermal and sound insulation, and works very well. I purchased metal studs and a tab-cutting interlock gun to join the studs together. Among my comprehensive tool kit, I have a percussion stud gun that uses .22 blank cartridges to drive 12D hardened nails through the anchor studs and plates into concrete floor, walls, and ceiling. To secure the 35mm thick cartongesso panels to the studs, I used self-drilling screws that countersink into the cartongesso. Recesses and joints were finished the usual way, with drywall compound as filler for the screw holes, and woven fiber tape and compound over the vertical joints. Overnight drying and a light scuff with sandpaper, and the walls were ready to paint. Trim from wood scraps then finished out door edges and baseboards.
The shop and garage were thus completed in 10 working days, working solo. The machines were pushed to the center of the shop and dust-covered. Once the wiring was completed and the walls painted, everything was cleaned off, pushed back into place and plugged in, and we were ready to go.
What a great feeling the first morning I walked down my driveway, hit the remote, and walked into a clean and well-lit workshop for the first time! I’ve been so busy since that day in April 2021, that it hasn’t been that clean since, though I really try, honest!